ディスクリート部品の製造工程では
印字時の粉塵が発生するためブラシなどで清掃する工程が必要になります。
|
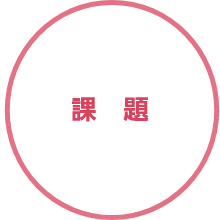 |
●粉塵が多く発生すると清掃工程が必要となりラインスペースを 圧迫することになる |
●清掃工程があることで、工程自体の管理工数やメンテナンス工数、 ランニングコストも増える。 |
●炭化物(粉塵)が周囲に飛び散ることでショートなどの不具合に つながる可能性が増える。 |
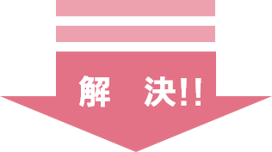
ショートパルスレーザーマーカーによる
優しい印字で煙や粉塵を削減
ショートパルスによる熱エネルギーを抑えた印字で、煙や粉塵の量をを削減することが可能です。
導入により清掃工程自体が不要になったという事例もあります。
※材質や印字の内容によっても結果が異なりますので事前テストが必要です。
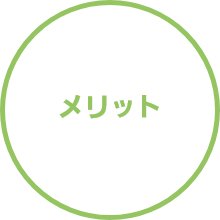 |
●粉塵量が減ることでショートなど不良のリスクも低減できる |
●清掃工程が削減でき、ラインスペースが確保できる 清掃工程がなくなれば、管理工数やランニングコストも削減できる
|
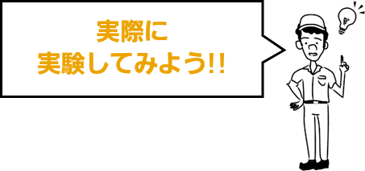
\ 粉塵削減効果の検証実験 /
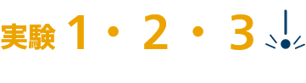
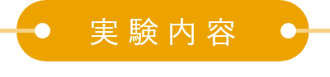
ディスクリート部品でよく使用される材質(PPS材・エポキシ材)に対して、 ①CO2レーザ、②ファイバレーザ(従来機種)、③ファイバレーザ(ショートパルスタイプ) の3機種にて印字実験を行ってみました。 |

【エポキシ材】
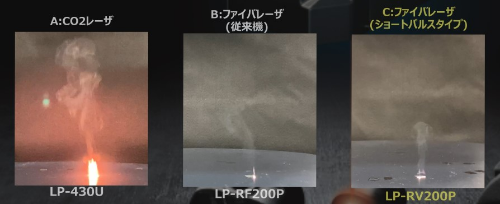
|
まずは印字時に発生する煙の量の比較です。 煙の発生量が多いと、集塵機のフィルタの目詰まりの周期が短くなり、頻繁に清掃や交換が必要となります。 また、清掃を怠ると設備内を汚したり、においなどの原因ともなります。
今回の実験結果ではPPS材/エポキシ材の両材質において A.CO2レーザの煙の量が多い結果となりました。 また、CO2レーザからファイバレーザにするだけでも煙の量の削減効果が見受けられますが、中でもショートパルスタイプは従来機に比べてさらに煙が削減できることがわかります。 ショートパルスによる煙の削減効果は特にPPS材への印字時に顕著に差が出ることがわかりました。 |
【PPS材】
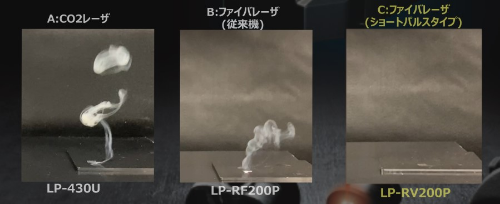
|

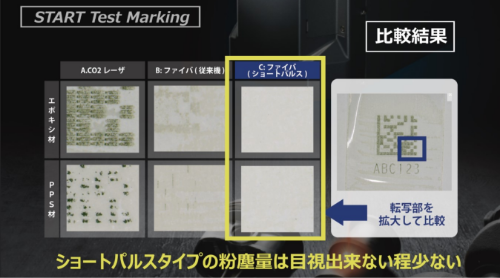 |
印字直後のワークに透明テープを貼り、テープに張り付いた 粉じん量を顕微鏡で比較しました。
こちらもPPS材/エポキシ材の両材質において、CO2レーザが最も粉塵量が多く、ファイバレーザ(ショートパルスタイプ)では目視確認できないほど減少することが確認できました。
|

|
最後に印字品質の比較です。 熱で掘り込みをするCO2印字と発色印字をするファイバレーザでは見た目が異なりますが、どのコードでも読み取りすることができます。
ショートパルスファイバレーザの印字はワークに与える熱影響を抑えることができ、焦げや変色が発生しにくく、コントラストが高い印字結果となりました。 |
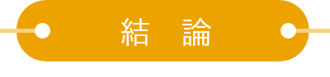
ショートパルスファイバーレーザなら CO2レーザや従来ファイバレーザに対して |
煙や粉塵量を削減することが可能!! |
 |
評価結果によっては清掃工程の削減に 繋げられるかもしれません。 |
|
カーボンニュートラルやSDGsのテーマとしても注目!
|
パナソニックのファイバレーザーマーカーは、CO2レーザマーカに比べて約1/3の消費電力で使用できるため、
近年ではカーボンニュートラルやSDGsなどのテーマにお役立ちできます。
廃棄ロス削減 |
消費電力が下がることで、CO2排出量削減につながります。 |
|
ランニングコスト削減 |
消費電力が下がることで、年間の電気代削減にもつながります。 |
消費電力の電気代・CO2排出量についての情報がまとめられています
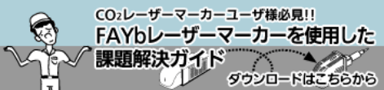
ショートパルスファイバレーザーマーカー”LP-RV”のカタログはこちらから

サンプルを用いた測定の実験や商品の仕様に関するお問い合わせはこちらから
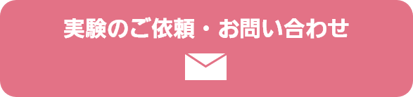